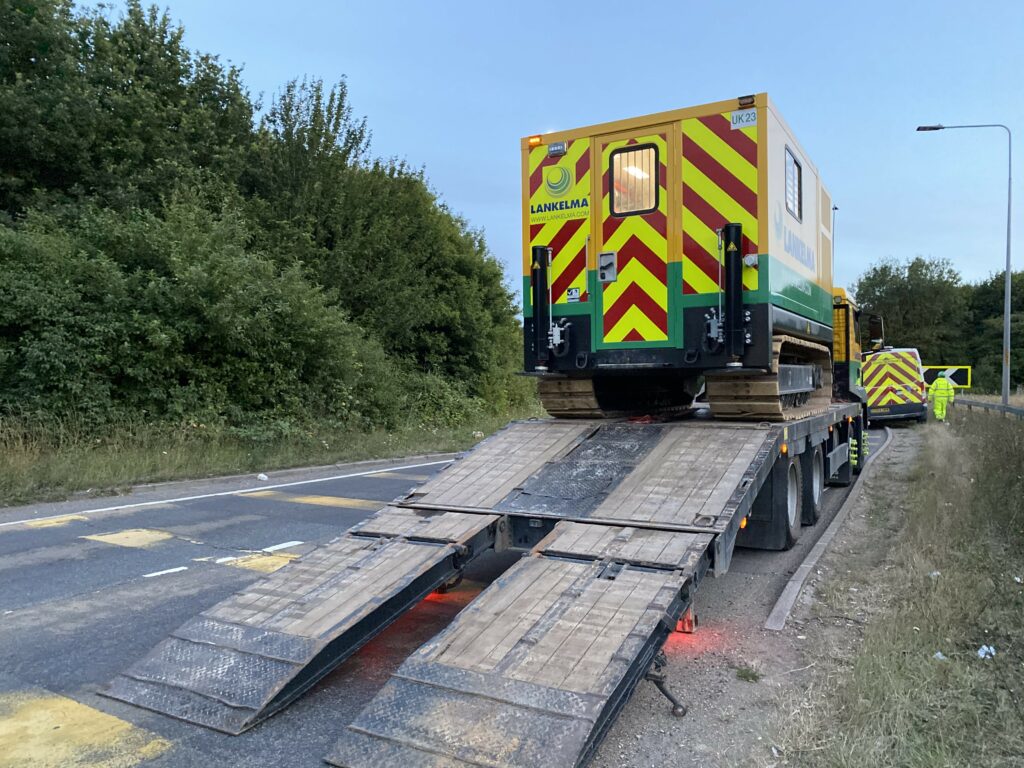
Introduction
In 2020, a government task force estimated that a third of all road traffic accidents involve someone at work. This accounts for potentially 20 fatalities and 250 serious injuries per week. Yet the rules on drivers’ hours, vehicle weights and licence requirements can be difficult to apply to specifics within your fleet. This article discusses how the ground investigation (GI) industry fits into the national legislation and how to ensure you and your colleagues are adhering to the law.
From 16th December 2021, the laws around towing a trailer changed to allow more licence holders the ability to tow without undergoing additional testing. This change was a government reaction to the HGV driver shortage, in an effort to free up examiner time, and whilst many individuals and organisations will be able to make the most of the new rules, it runs the risk of adding more uncertainty to an already misunderstood set of laws.
What the legislation tells us
A simple rule of thumb is if the sum of the vehicle and trailer weight is less than 3.5 tonne, then the driver would probably fall under domestic drivers’ rules. The main restrictions under these rules are a limit of 10 hours total driving or 11 hours duty time per day. There is a list of exemptions to this categorisation, so it’s important to correctly identify your vehicles along with the intended activities.
If your vehicles and/or trailer weights are over 3.5 tonnes, then EU rules can apply (with some exceptions). This will likely mean the introduction of tachographs within your vehicle cabs and potentially even operator licencing for your company. These are requirements used throughout the haulage and logistics industry to safely manage the operations of large goods vehicles across the continent. However, this can prove difficult to apply in the GI industry without the help of a transport manager or a competent person experienced with the level of compliance needed.
Many small-to-medium enterprises will have to make difficult choices of whether to use costly third-party couriers for their equipment mobilisations, or to fund both the training of employees and capital investment needed to comply. This will inevitably lead to instances of non-compliance, either consciously or subconsciously, when driving an overweight vehicle or to travel five hours to the next job after a full day on site.
Learning Lessons
Following several instances of rail workers being involved in road traffic accidents on the drive home after a night shift, new fatigue management regulations were adopted. This included recommendations on shift times per day and week, along with minimum rest periods and importantly, the time spent travelling to and from work. Employers are urged within the guidelines to ‘assess and control work related road risks in their operation’ as the travel time can ‘contribute to fatigue’. Possible solutions include providing nearby lodgings or safe transport, such as a taxi.
Requests from the Principal Contractors for staff location and travel times are subsequently commonplace for shift planning within the rail industry. Is it time for similar requirements to exist across the GI industry?
We all hear the stories of 4am starts for field workers in order to reach site for the inductions at 8am and/or getting home at 10pm on a Friday night, but with the alternative being weekend travel disrupting the work life balance and increasing costs, it’s easy to see why these practices have become the norm. If we’re going to ensure all workers attending our site have the right class of cut resistant gloves or the correct CPCS card for the plant their operating, should we not also check they haven’t driven 300 miles that morning?
Accreditation bodies such as the Fleet Operator Recognition Scheme (FORS) offer their members an opportunity to showcase their adherence to a high standard in terms of transport management and can be assurance to contractors that their supply chain invests in the correct practices. However, from experience, it is not straight forward.
What we can do
The ability to apply the legislation to the specifics of your own business is key, to shine a light on the grey areas we often find ourselves in, or in some instances look to put ourselves in. Given recent changes in licencing, it’s important to familiarise yourself with the current rules.
Firstly, identify and categorise your fleet to ascertain the specific restrictions of your vehicles when laden with equipment. Secondly, confirm the licencing and competence of the intended drivers. Then plan your work schedule accordingly to allow for at least the minimum breaks and driving hours as required by law.
Logistics have come a long way since the days of AA route planners. There are dozens of software packages available to help organise your vehicles, drivers, and their movements, and importantly, to ensure compliance. Many can be adjusted to suit your specific needs and are often scalable to help with the cost/benefit ratio.
Do not underestimate the importance of monitoring driving activities within your business. You can identify gaps in either driver or management competencies and take action to introduce safer practices. In the event of a work-related road traffic accident, a major focus of an investigation will be on the records kept; driver competencies, along with tachograph records or employee timesheets, help to establish not only how events unfolded, but also determine any unsafe practices. By monitoring, you are providing evidence that unavoidable exceedances of driving hours, for example, are recorded and lessons can be learnt.
Summary / Conclusions
The HSE Driving at Work guidelines make it clear that ‘on the road work activities and the risks should be effectively managed within a health and safety system’. This means imbedding policies and procedures within an organisation to manage the risks and associated measures.
Becoming a member of industry bodies such as the Road Haulage Association or Logistics UK, not only keeps you up to date with any changes in the law, but also enables you to call on experts for advice on how best to manage your fleet.
Managers and senior staff should lead by example. By having a thorough understanding of the legislation, good practices can be employed, demonstrating an expectation within the business. Investment in maintenance and training to ensure your fleet is safe and legal is also imperative. Further, good communication between management and field workers regarding shift patterns or fatigue, either with themselves or colleagues, as well as reporting any accidents, incidents or near misses is crucial to implementing a positive change.
Article provided by Chris Dimelow, Operations Director, Lankelma