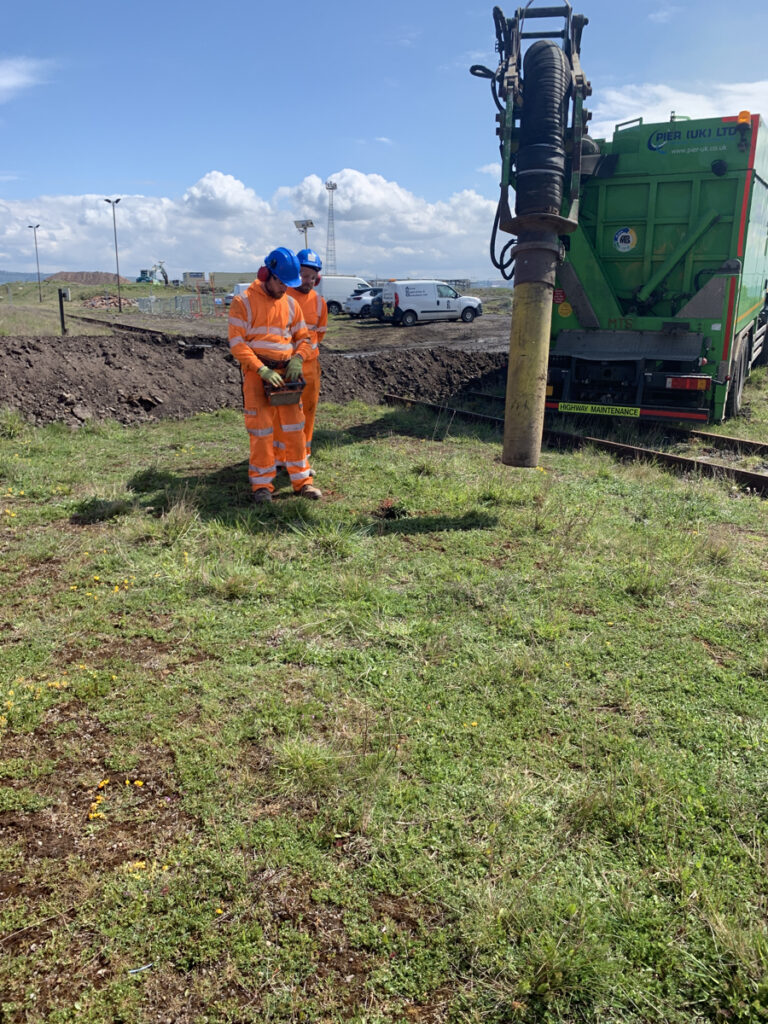
Vacuum excavation[1] is widely used in the ground investigation industry as a means of excavating inspection holes and trenches to check for utility services prior to drilling or probing. The significant safety benefits of vacuum excavation compared to hand digging are that the operatives are not as close to any exposed utility services and that the hazards associated with damage to utility services by hand-held digging equipment are significantly reduced from the activity, a true reduction of risk through engineering controls.
Urban and brownfield sites typically contain made ground and industry suggests that asbestos is detected on most brownfield sites that are investigated[2]. A recent SOBRA report indicated that the asbestos detection rates in soil samples submitted for laboratory analysis vary from 1.4% to 20%[3]. SOBRA concluded that: ‘Anecdotal information from the industry suggests that asbestos is detected at the majority of brownfield sites that are investigated. This data suggests that, on average, asbestos is detected in a small (but nevertheless potentially significant) proportion of samples from those sites.’ Excavation on brownfield sites could therefore encounter asbestos in soil both as visible asbestos containing material (ACM) or as loose fibres, which are not visible to the eye.
The Construction Plant-hire Association (CPA) guidance1 states that if asbestos is suspected during vacuum excavation, work should stop so advice can be sought, and that disturbance of asbestos should be prevented. It suggests that suitable documented control measures and in some cases specialist or dedicated suction/vacuum excavator machines are required for the removal of asbestos impacted soils.
To comply with the Control of Asbestos Regulations 2012, CAR-SOILTM and AGS Guidance, the CPA recommended that where asbestos is suspected additional controls should be introduced which include: use of suitable PPE and a grade P3/FFP3 face mask; working with a water lance (not air lance) which is less likely to cause asbestos fibres to become airborne; cleaning and disposal of outer clothing; good hygiene; and decontamination of the machine. The guidance indicates that if asbestos was seen, a laboratory could attend site and undertake monitoring of the machine’s exhaust air, at the downwind public boundary, as well as personal monitoring and swab testing of the machine including the filter. These control actions are reliant on the presence of asbestos being identified or suspected by the Vacuum Excavation operatives or pre-notified to them.
As asbestos in soil can be difficult to identify and loose fibres would not necessarily be visible to the naked eye, the principles of the Construction Design and Management Regulations 2015 (regulation 12.2 including Schedule 3 & 12.4) should be followed. Those employing vacuum excavator should set out the arrangements for controlling risks within the construction phase plan, Schedule 3 ‘Work which puts workers at risk from chemical or biological substances constituting a particular danger to the safety or health of workers or involving a legal requirement for health monitoring’. In addition, where members of the public could be at risk from vacuum excavation of impacted soils within an urban or residential setting, the requirements of the Health and Safety at Work Act 1974 Section 3 ‘General duties of employers and self-employed to persons other than their employees’.
It is therefore a requirement for any contractor adopting vacuum excavation to provide to sub-contractors suitable and sufficient information about the risk of asbestos being present within the target area soils and the controls required to mitigate this risk.
Therefore, for those proposing to use vacuum excavation in environments where soils contain or are suspected of containing asbestos; it is recommended that:
- they notify operators of the vacuum excavation equipment of the presence (or potential presence) of asbestos in the soil.
- they consider adopting mitigation controls (in addition to those identified by CPA described above) such as would be required for asbestos in soils environments e.g. using controlled wetting, mist curtains, etc.
- the control measures within the CPA guidance are adopted for all brownfield sites until the risks to workers and the public from airborne asbestos resulting from the use of suction/vacuum excavators are better categorised; and
- asbestos in air monitoring is undertaken to support the use of vacuum /suction excavators on brownfield sites including both personal monitoring, boundary monitoring and monitoring of exhaust air to better understand the risk levels to workers and the public.
The CPA guidance suggests that exhaust air emissions could impact other workers and the nearby public, highlighting that the type of filtration used within vacuum excavators does not capture and contain asbestos fibres. While it is possible to dampen the soils entering the vacuum excavator, the mechanical action of the vacuum causes the excavated soil to be dried and could therefore facilitate fibre release, both at the location being excavated and also at subsequent sites using the same plant, prompting a need for thorough decontamination of the plant (in line with the requirements of the Control of Asbestos Regulations 2012) when it is used to extract asbestos impacted soils.
The management of waste is also a consideration when undertaking vacuum excavation where the presence (or potential presence) of asbestos in the soil is known. In such a scenario, the extracted material and plant decontamination washout, cleaning and swabbing materials should all be treated as waste, handled, transported, and disposed of in line with legislative requirements.
The use of vacuum excavators to expose utility services or to disprove the presence of utility services remains a lower risk than conventional machine and hand dug excavation and remains a preferred excavation method when excavating made ground with on urban or brownfield sites where there is a risk of utility services. However, careful planning of these activities is required to ensure that the significant physical risk posed by the utility services is not replaced by a significant health risk posed by potential asbestos release.
By following the principles of good task planning; communicating potential risks, assuring safe systems of work, waste control and staff competence, suitable and sufficient risk mitigation for the use of vacuum excavators on made ground can be achieved.
There will, however, be some conditions which limit the ability and effectiveness of these controls measures to mitigate the risk of asbestos, especially when working within heavily populated areas. In such cases careful evaluation of available risk controls effectiveness is required.
[1] Industry guidance ‘Safe Use of Suction/Vacuum Excavators, Good Practice Guide, Construction Plant-hire Association, Safety Publication Series, SAVESIG GPG1, January 2019’ describes suction/vacuum excavators as ‘items of plant utilising a powerful fan or pump to cause a pressure reduction in a suction hose in order to excavate pre-loosened earth and granular materials, and draw them into a temporary store in a receiving hopper for subsequent discharge. As the spoil reaches the hopper, it is separated from the moving air by cyclonic and other filtration methods, with cleaned air exhausted via an outlet system whilst the spoil is contained within the sealed hopper.’ Ground engaging tools that break soils can be utilised with suction/vacuum excavators and ‘air or water pressure through a lance is considered a safer system than manually breaking soils and allows quick and easy displacement of material around sensitive areas of services. The use of a lance minimises the need for the operator to be at the edge of or within an excavation.
[2] The Distribution of Asbestos in Soil – what can the data mining of sample results held by UK laboratories tell us? Discussion Paper by the SoBRA asbestos sub-group, March 2020
[3] The March 2020 SOBRA paper considered asbestos test results from five laboratories across different time periods since 2011. The origin of the soil samples was not known, and the test methods varied.
Article by Madeleine Bardsley, Technical Director at WSP and Jon Rayner, Director SH&E at AECOM
Image credit: AECOM