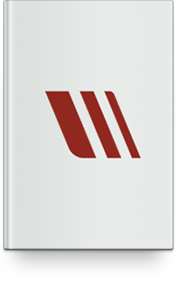
Published May 2023. This version replaces ‘AGS Guidance on Manual Handling’ published in 2019.
Incorrect manual handling is one of the most common causes of injury at work. It causes work-related musculoskeletal disorders (MSDs) which account for over a third of all workplace injuries. Heavy manual labour, awkward postures, repetitive handling tasks, manual materials handling (i.e. handling, moving and lifting bulk samples) and previous or existing injury are all elevated risk factors in developing MSDs.
Poor work area set up can lead to increased manual handling and increased risk of manual handling injuries due to the loads being handled, the distance they are handled, the frequency at which they are being handled and the environment they are being handled within.
Ground Investigation activities consist of many operations which rely on manual handling to complete work tasks, either in its entirety or as part of the overall work process.
The Manual Handling Operations Regulations 1992 (MHOR) require employers to manage the risks to their employees. They must:
- Avoid hazardous manual handling operations as far as is reasonably practicable, by redesigning the task to avoid moving the load or by automating or mechanising the process.
- Make a suitable and sufficient assessment of the risk of injury from any hazardous manual handling operations that cannot be avoided.
- Reduce the risk of injury from those operations so far as is reasonably practicable. Where possible, provide mechanical assistance, for example, a sack trolley or hoist. Where this is not reasonably practicable; explore changes to the task, the load and the working environment.
It is best practice to prevent the need for manual handling, however, when not possible consideration needs to be paid as to whether or not the activity is critical or not. If the activity must be carried out all hazards must be adequality controlled to mitigate the risk of injury.