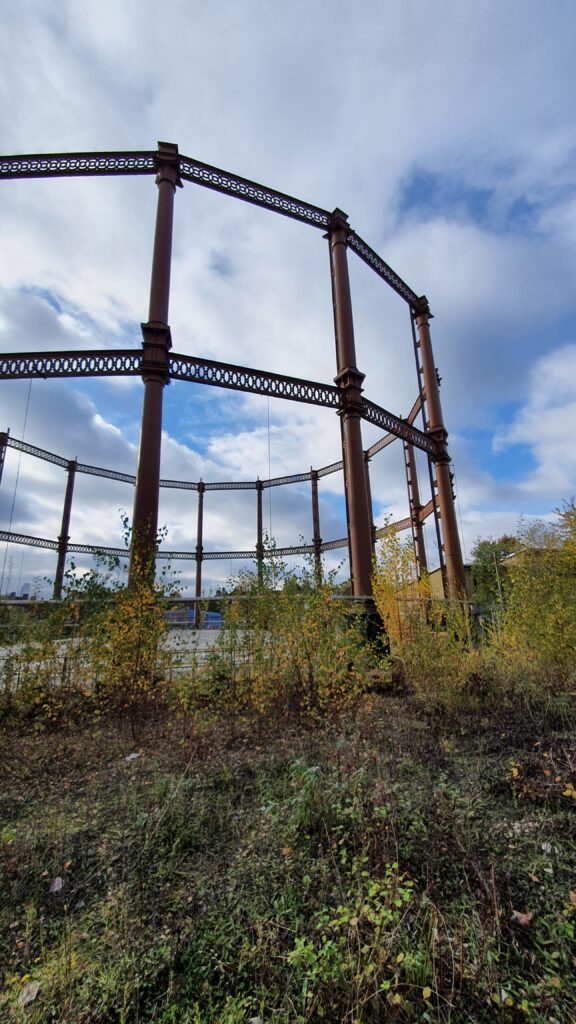
Biodiversity net gain (BNG) is an approach to development that aims to leave biodiversity in a measurably better state than before. BNG is both an outcome and a process. The approach to BNG consists of ten guiding principles as outlined in the Good Practice Principles for Development[1] and in England, the application of an excel-based tool, the Biodiversity Metric 3.1 Calculation Tool[2] (hereafter ‘the Metric’), as a proxy measure of biodiversity. In this article, we will explore how the Principles for Development are essential to the best practice application of the Metric to avoid biodiversity being considered as a numbers game. We will also discuss the opportunities and risks presented by BNG and its delivery to the development of brownfield land.
Across the UK, the BNG approach is known and associated with policy and legislation to different degrees. In England, the Environment Act 2021 has made the BNG approach a mandatory requirement of planning permission. This primary legislation requires all size developments, excluding permitted development, to achieve a minimum of a 10% net gain in biodiversity for at least 30 years, demonstrated through the Metric. It will come into effect between 2023 and 2025 and tie in with secondary legislation providing further details of how the approach will work in practice. In the meantime, Local Planning Authorities already expect net gain to be achieved in developments, as required by the National Planning Policy Framework (NPPF); the difference being that the NPPF does not define a percentage.
In Scotland, Wales and Northern Ireland, legislation for BNG does not yet exist. Current policy, however, suggests the use of BNG as a valid and robust way to meet policy requirements. For example, in Scotland, the latest National Planning Framework 43 must implement the Planning (Scotland) Act 2019 stipulation for development to secure positive effects for biodiversity[3]. In Wales, under the Planning Policy Edition 11, there is the requirement for development to prevent biodiversity losses or compensate for losses where damage is unavoidable[4] and that any development must provide a net benefit for biodiversity. In Northern Ireland, Planning Policy Statement 2: Natural Heritage 2013 states ‘planning policies of this statement must have regard to any strategy designated for the conservation of biodiversity…’ and ‘protection and/or enhancement’ of ‘natural heritage features and designated sites’ is required[5].
This article will focus on England, where policy and legislation are most developed in BNG, allowing for better exploration of implications for brownfield land. However, many of the principles of how the approach works, as well as drawbacks and opportunities, could apply elsewhere in the UK.
Initially, Natural England, the relevant non-departmental public body, considered whether brownfield land should be excluded from the Metric. However, following a recently completed consultation[6], the government is proposing not to apply exemptions to brownfield sites that meet a set criteria. They state that ‘an exemption based on an appropriate combination of these criteria would deliver little added benefit and would greatly complicate the requirement’s scope for developers and planning authorities alike…. furthermore, many brownfield sites offer significant potential for achieving biodiversity net gain as they often have a low pre-development biodiversity value’[7]. Therefore, brownfield developments are seen to offer significant biodiversity value, especially in urban environments.
The habitats found on brownfield land vary from areas of remaining bare ground or hard standing, to ruderal and ephemeral vegetation, to grassland and scrub. Where a combination of these habitats occurs within a certain continuous area, they can fit the description of Open Mosaic Habitats on Previously Developed Land (OMH). The periodic disturbance and abandonment of the land replicates the ‘disturbance’ process found in natural ecosystems. Disturbance is often essential to ‘restart the clock’ of succession (the process by which the structure and mix of species and habitats in an area change over time). Disturbance supports the creation of a variety of habitats across a landscape, which in turn supports species diversity. This is where brownfield land can be valuable to biodiversity.
Brownfield land often falls into the category of a biodiversity rich habitat or one that is very poor for biodiversity. The type of species and habitats found on brownfield land are often rarer than those found in the countryside, with evidence suggesting between 12% and 15% of all nationally rare and scarce insects are recorded on these sites[8]. Whilst the countryside is often viewed as more biodiverse, many modern farming methods prevent the establishment of diverse habitats and species. Therefore, often brownfield land is more bio-diverse than the farmed countryside.
Where brownfield land does not have OMH and is classified as poor quality, it can offer significant opportunities for habitat banking. Habitat banks are habitats that are created in advance of development i.e., banked for later. When a development goes ahead, and the habitat can’t be saved, the habitat bank can be called upon to offset the habitat lost providing the previous steps of the mitigation hierarchy have been applied[9]. There are various opportunities with brownfield land to provide a bank. Where low scoring brownfield habitats are present, such as with hardstanding, bare ground or certain ruderal, ephemeral, grassland and scrub types, much can be done to improve biodiversity. For example, taking up the hardstanding to plant, planting up bare ground, adding more native species variety to existing grassland or scrubby areas, or adding a range of habitats instead of one.
As habitat banking is in its infancy, expert advice is necessary before setting up a habitat bank to ensure that the correct governance, registration (with the LPA but likely also with NE) and monitoring procedures are in place to meet the Environment Act (2021) requirements. Currently, there is no regulation around habitat banking; regulation is expected between 2023 and 2025 when BNG will become mandatory.
When brownfield land has low scoring habitats of condition and distinctiveness, they can be used to contribute toward a development project to achieve net gain, as they can be replaced with almost any other habitat and result in significant biodiversity improvements. This is providing that they are not OMH or other priority habitats i.e., some ponds or native woodland. For example, a site consisting of one hectare area of bare ground provides 2 biodiversity units according to the Metric. Should two-thirds be lost to development and the remainder landscaped with native scrub, 2.21 units could be provided, making a 10% net gain.
In the UK, there is a focus on the remediation of brownfield sites. However, remediation can decrease habitat diversity if it involves intense management instead of natural processes. The addition of nutrient rich topsoil and seeding grass species that require intense management regimes homogenises sites, decreasing plant and animal diversity. Where remediation is not considered, brownfield sites are often neglected and result in scrub encroachment, which can in some cases reduce biodiversity.
High quality brownfield sites may be OMH, which must be considered separately. As a mosaic habitat it may include other habitats of principle importance and is not easily defined so its definition depends on meeting a number of quality criteria. It can be made up of a wide range of habitats including grassland, tall ruderal plant species, native and non-native invasive species and early pioneer communities and is particularly valuable to rare and declining invertebrates[10]. They are vital in ensuring high levels of biodiversity in the UK, supporting pioneer species and species that move between habitat patches, and providing refuge for others. OMH is a Habitat of Principle Importance under Section 41 of the Natural Environment and Rural Communities Act 2006 due to its ability to support a rich assemblage of invertebrates. To qualify it needs to be at least 0.25ha, have more than one specified habitat type within the mosaic, and meet other specific criteria including a known history of disturbance at the site[11].
Within the Metric, OMH is assigned a high ‘distinctiveness’ level. Distinctiveness is a term used in BNG to describe innate qualities of a particular habitat type and can range from very low to very high. Due to the high distinctiveness of OMH, encountering a site with OMH can be problematic for the developer. Instead of losing and needing to replace 2 units/ha (as would be the case for bare ground), losing OMH habitat would result in the loss of at least 6 units/ha. OMH must also be replaced with the same habitat. Finally, OMH is considered to be of medium difficulty to create in the ‘difficulty to create’ risk factor of the Metric, meaning that it will likely only be successfully created two-thirds of the time. Thus, the Metric requires 1ha of lost OMH to be replaced with 1.9ha of the same habitat of the same quality.
One of the aims of the Metric is to disincentivise development on particularly valuable habitats, which might occur with OMH. However, though it is difficult to create, other habitats in the Metric are considered harder to create. OMH may also be easier to manage: because the habitat is a result of previous disturbance, more disturbance can be used to ‘reset its clock’. This could be as simple as clearing areas rotationally from time to time. Also, this habitat is only considered to require four years to reach moderate condition in the ‘time to target’ risk factor of the Metric, and ten years to reach time to target good condition. However, the site would need to be managed for 30 years under the Environment Act. It should be noted that each site is unique and there is no set time period in which OMH will develop. This period is dependent on various factors like the type of brownfield site, proximity to other landscape features, topology and climate. Furthermore, because the distinctiveness of the habitats is high, they produce high numbers of biodiversity units relative to their area. Finally, these areas punch above their weight in biodiversity terms compared to other habitats and can be particularly valuable in urban areas where other greenspace is lacking. For these reasons, OMH could be a good habitat to investigate when setting up a habitat bank.
The government has identified that at least 300,000 new homes would need to be built in order to meet the increasing housing supply demands. It recently announced an initiative to promote the development of derelict sites into new homes under a new brownfield fund[12]. Whilst this is viewed as a way to boost local economies and home ownership, there is a significant risk to biodiversity and ensuring climate resilience within cities. Research has shown that ex-landfill sites contain assemblages of rarer birds, which could be lost through new housing developments (Macgregor et al., 2022)[13].
There are several opportunities associated with this type of habitat, including the multi-functionality of these sites and the creation of habitats from the start of the succession, thus supporting more biodiverse pioneer species than had previously occurred. Additionally, naturally occurring OMHs, which develop as a result, will enhance biodiversity in a fragmented landscape through the creation of habitat corridors, which will have an overall significant beneficial impact on future biodiversity.
In conclusion, brownfield sites, through the presence of OMH, can have greater biodiversity than that of countryside land and other land within the UK, as shown through the Metric. This increased biodiversity uplift in both condition and distinctiveness occurs through the development of OMH on brownfield land that is in a poor condition. However, to realise these benefits, further awareness is required including the correct management regime of these sites and to increase the public and developers’ perception of the benefits of these sites. OMH provides vital successional habitats for a wide variety of species if the natural ecosystem process is allowed to occur. These habitats are Habitats of Principle Importance and are key to enhancing biodiversity, climate resilience and wider natural capital benefits. These sites have commercial potential through offering habitat credits (i.e., a unit of trade that places monetary value on habitat preservation or restoration[14]) to both developers and Local Planning Authorities via the creation of habitat banks. However, allowing OMH to occur on these sites is not considered in line with the current government plans to build new homes and boost the local economics.
References:
[1] CIEEM, CIRIA, IEMA (2016) ‘Biodiversity Net Gain: Good practice principles for development
https://cieem.net/resource/biodiversity-net-gain-good-practice-principles-for-development/ Biodiversity-Net-Gain-Principles.pdf (cieem.net)
[2] Natural England (2022), The Biodiversity Metric 3.1. The Biodiversity Metric 3.1 – JP039 (naturalengland.org.uk)
[3] Planning (Scotland) Act 2019 [online]. Available at: https://www.legislation.gov.uk/asp/2019/13/section/2/enacted
[4] Welsh Government. Planning Policy Edition 11 [online]. Available at: https://gov.wales/sites/default/files/publications/2021-02/planning-policy-wales-edition-11_0.pdf
[5] Department of the Environment (2013). Planning Policy Statement 2 Natural Heritage [online].
Available at: https://www.infrastructure-ni.gov.uk/publications/retained-planning-policy
[6] Department for Environment Food & Rural Affairs (2022) ‘Consultation on Biodiversity Net Gain Regulations and Implementations. https://consult.defra.gov.uk/defra-net-gain-consultation-team/consultation-on-biodiversity-net-gain-regulations/ (accessed 01/08/222). Results expected Autumn 2022.
[7] Department for Environment Food & Rural Affairs (2022) ‘Consultation on Biodiversity Net Gain Regulations and Implementations. https://consult.defra.gov.uk/defra-net-gain-consultation-team/consultation-on-biodiversity-net-gain-regulations/ (accessed 01/08/222). Pg 26.
[8] Lush.M., Kirby.P., & Shepherd.P. (2013) ‘Open Mosaic habitat survey handbook’ Open Mosaic Habitat Survey Handbook (buglife.org.uk) (accessed 29/07/22).
[9] Chartered Institute of Ecology and Environmental Management (2021) ‘Good Practice Requirements for Delivering Biodiversity Net Gain (On-and Off-site)
[10] https://www.nature.scot/sites/default/files/2018-02/Priority%20Habitat%20-%20Open%20Mosaic%20Habitats%20On%20Previously%20Developed%20Land.pdf#:~:text=The%20Open%20mosaic%20habitats%20on%20previously%20developed%20land,sites%20support%20good%20examples%20of%20this%20priority%20habitat. (accessed 01/08/22)
[11] Riding, A., Critchley, N., Wilson, L. and Parker, J. 2010. Definition and mapping of open mosaic habitats on previously developed land: Phase 1. Defra Research Report WC0722. London, Department for Environment Food and Rural Affairs.
[12] Department for Levelling Up, Housing and Communities (2022). ‘Derelict sites to be transferred into new homes as new brownfield sites opens’ https://www.gov.uk/government/news/derelict-sites-to-be-transformed-into-new-homes-as-new-brownfield-fund-opens (accessed 29/07/22).
[13] Mcgregor.C., Bunting. M., Deutz.P., Bourn.N., Roy.D., Mayes.W. ‘Brownfield sites promote biodiversity at a landscape scale. Science of the Total Environment, Vol 804, Jan 2022, 150162.
[14] Garnter.T., (2010) ‘Habitat Credit Trading’ PERC Reports, Volume 28, No.1.
Article provided by Hannah Williams (Principal Ecologist, BNG) & Harriett Ricketts (Natural Capital Specialist) – WSP
Image credit to Andy O’Dea, Cognition Land and Water