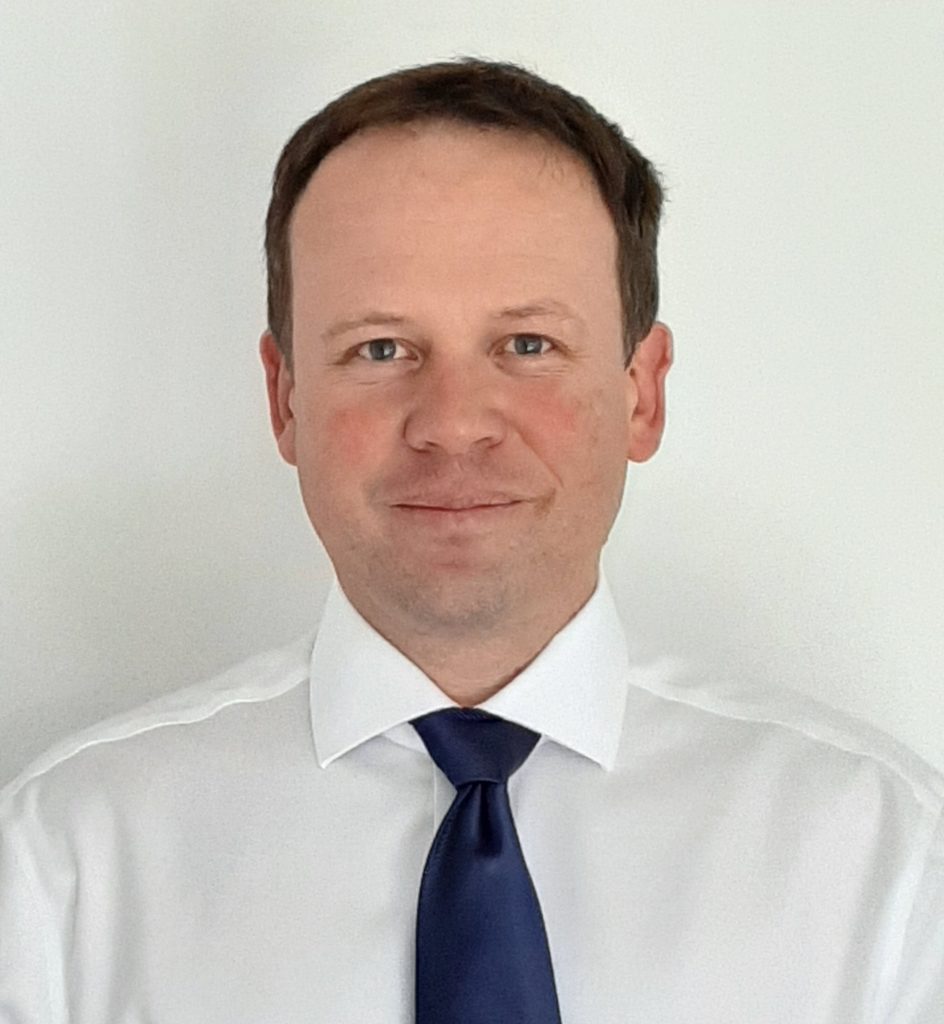
Full Name: Geraint Williams
Job Title: Associate
Company: ALS
Geraint has over 20 years’ professional experience and is technical lead for his company. He is a member of the AGS contaminated land and laboratories working group. He serves on the Executive Committee of the Society of Brownfield Risk Assessment (SoBRA) and participates in specialist groups including SoBRA’s vapour intrusion subgroup as well as chairing SoBRA’s Technical Panel. Geraint also serves on EH/4, the British Standards committee on soil quality and is chair of a drafting panel for a new standard on sampling soil for determination of volatile organic compounds.
What or who inspired you to join the geotechnical industry?
My father inspired me to be involved in our industry. I remember travelling to nearby Wirral where he pointed out interesting geological features including the ‘Red Rocks’ at Hoylake.
What does a typical day entail?
I spend lots of time supporting my teams, through technical review, dealing with clients’ challenges and troubleshooting when issues inevitably arise. Training and mentoring colleagues is important and also the most rewarding aspect of my job.
Are there any projects which you’re particularly proud to have been a part of?
I spent the formative years of my career carrying out intrusive investigation work for McAlpine on a major gas pipeline project in the North West which was an excellent grounding for anyone starting out in our industry. I’ve been fortunate enough to be involved in the largest land contamination projects in the UK.
I’ve been involved in projects in the Occupied Palestinian Territories, Afghanistan, Kuwait, Ivory Coast, and Nigeria. I was in Iraq recently training those who are managing the investigation and remediation of sites that experienced widespread destruction from sabotage and looting by Islamic State. The impacts of war in eastern Mosul are so extensive that much of the old city has essentially been destroyed. It is a privilege to be part of reconstruction efforts in conflict affected areas of the world.
What are the most challenging aspects of your role?
Being away from my family – I spent a month in West Africa when my daughter was first born. She is now eight so probably won’t notice if I spent six months away from home!
What AGS Working Group(s) are you a Member of and what are your current focuses?
I’m a member of the Contaminated Land Working Group – we have recently produced practitioner guidance on waste classification for soils, description of anthropogenic materials and environmental sampling.
What do you enjoy most about being an AGS Member?
I genuinely look forward to every meeting as it provides an opportunity to discuss matters that directly affect our industry. It’s a forum for knowledge sharing and promoting best practice. I most enjoy the technical aspects of our meetings and the collaborative way we work together to overcome common issues and challenges.
What do you find beneficial about being an AGS Member?
The AGS is the only organisation representing both the interests of the geotechnical and geoenvironmental sectors. It’s beneficial how different working groups come together to tackle issues – asbestos is a good example of Contaminated Land, Labs and Safety Working groups co-ordinating their efforts to each have input into what will become pragmatic guidance.
Why do you feel the AGS is important to the industry?
AGS provides its members with a real voice within industry – we are active on the National Brownfield Forum, we are represented on the Phase 2 Category 4 Screening Level Project and are involved in updating the Guiding Principles; our membership includes the Environment Agency and the National House Building Council. We probably don’t appreciate how respected and influential the AGS actually is. I suspect this will only increase as focus is shifting more towards industry-led guidance.
What changes would you like to see implemented in the geotechnical industry?
Like most of us, I’d like to see government implement a truly brownfield first policy. Our sector is worth £1 billion a year and employs almost 10,000 people. The housing crisis is one of the UK’s greatest challenges and brownfield development is key to solving it. No surprise that AGS is at the forefront of highlighting these challenges and making positive steps to address them. If you haven’t seen it, read the article ‘Unlocking complex brownfield sites’ in a previous edition of this magazine.